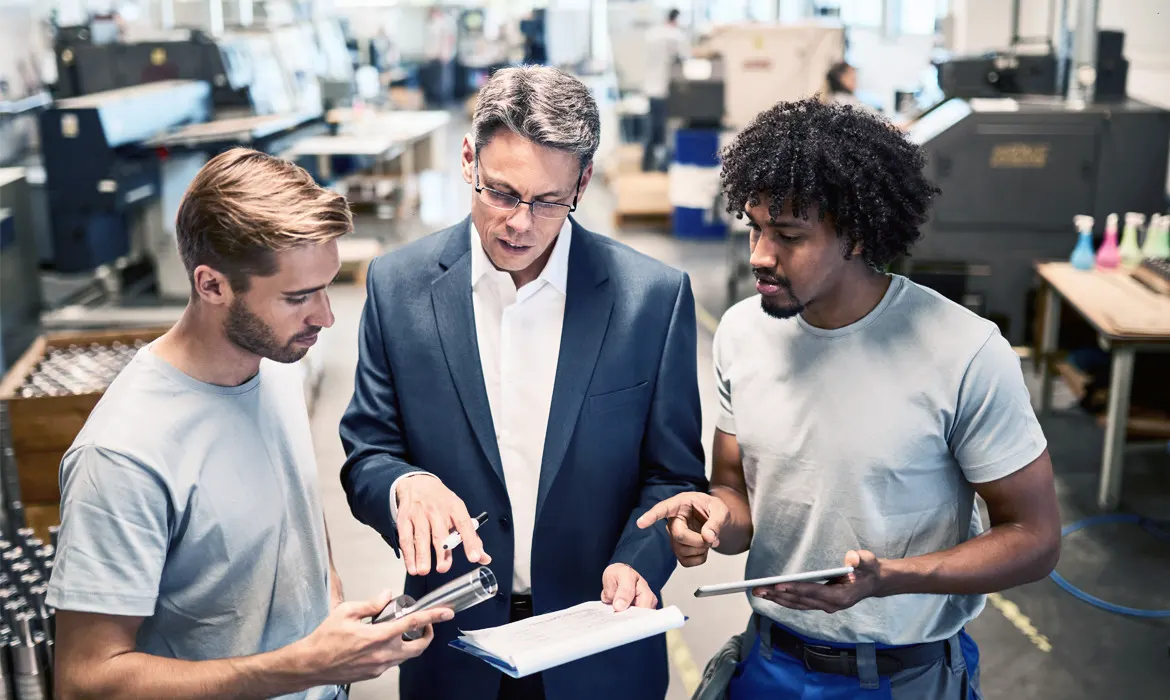
1. Who is and what does a Flying doctor do in the Automotive sector?
The Flying doctor is a professional with proven experience and strong analytical skills able to intervene on a specific component and inform all those involved in the production phase about any defects found, about their seriousness and if it is necessary to replace, or more simply repair, the analyzed component.
The Flying Doctor activity (also called Man in the Van to avoid confusion with the Australian medical service) is a service aimed at the automotive warranty between manufacturer (OEM) and supplier (TIER1) which plays a strategic role in improving the main KPIs.
Therefore, the action of a Man in the Van takes place mainly on the side of the dealer or authorized workshop belonging to the car manufacturer's Service chain, going to carry out the analysis of the alleged defect.
Given the high level of professionalism required, the extensive experience gained and the willingness to travel even intercontinentally, companies in the automotive sector now prefer to turn to independent flying doctors, such as those at Punto Netto, rather than meet this need by identifying personnel within their corporate organization, thus increasing the costs of the service without guaranteeing maximum efficiency.
2. What skills must a Flying doctor have and what knowledge must be received from the customer?
A Flying doctor must have developed solid technical skills in the automotive sector in compliance with the IATF 16949 standard, which is the cornerstone of the general rules through which car manufacturers manage quality and the related and possible complaints.
He must be available for business trips, in many cases speak the language of the place where he will intervene and possess an excellent capacity for synthesis in intervention reports and reports.
Furthermore, he must be willing to receive adequate training at the plant that produces the components that he will then analyze, in order to have perfect knowledge of the production processes and communicate with the parent company when he will presumably be at work at the dealerships.
3. What are the most requested training areas for Flying doctors in Automotive?
- Component training
It is generally entrusted to the technical body which transfers the characteristics of the product and the areas of operation for which that particular component was designed. It is useful to remember that in the automotive sector, the components are co-designed and the technical request comes from the car manufacturer. However, the supplier makes its technologies and skills available to improve the product or identify the presence of critical issues
- Production line training
This type of training provides the Man in the Van with adequate knowledge of component assembly processes. Generally these are entrusted to the production body which transfers which products and which steps are necessary to make the component. Knowing how the product happens, can help a lot to indicate which assembly phase may have generated a defect
- Training on known quality issues
Transferring the largest sample of defects that have already occurred to a Flying doctor makes field intervention faster and the description of the defect more precise. It is also important to transfer the defects found on the incoming products mounted on the component to the operator in order to be able to indicate defects on external supplies. It is of the utmost importance to transfer the defects recorded during operation or after returning from the workshops to monitor the recurrences of defects on the network
- Training on fault diagnosis
The diagnosis of an apparently simple mechanical component can involve complex areas such as metallurgy, mechatronics, fluid dynamics, which require dedicated diagnostic equipment and knowledge of its correct use. The ability of a Flying doctor to transmit the outcome of a correct diagnosis of a new defect allows the manufacturer to can quickly start a non-conformity containment action on a well-defined and detected area
4. What are the workplaces of a Flying doctor in the automotive sector?
Usually, the Man in the Van is assigned a geographical area whose extension depends on:
1. by the number of authorized dealers and workshops belonging to the car manufacturer's Service chain
2. by the number of cars of the manufacturer circulating in that territory
3. the average number of cases per month that need to be managed
They can cover one or more provinces of a given country but also an entire state. It is evident that, when such extensive territories are assigned to a Flying doctor, it means that the number of qualitative accidents of the supplier are minimal or that the car manufacturer's Service chain is scarcely present in that area.
There is something to keep in mind that the Flying doctor periodically returns to the component production plant for new refresher courses, but also to jointly analyze with the factory Quality Service the parts that have been sent back. This is because it is very important that the judgment in the field of a Man in the Van, when confirming the non-conformity of a component, and the judgment in the factory of the quality body that receives that scrap piece, agree in the same evaluation.
5. What are the benefits of organizations using a Flying doctor?
The advantages that automotive suppliers obtain from the use of an external Flying doctor are mainly economic. But the use of such a professional figure also has important repercussions on strengthening the brand identity of the manufacturer.
To fully understand this statement, we would like to point out some topical cases that the Punto Netto Flying doctors have identified in recent years:
• The first concerns a supplier of shock absorbers which is accused of a high percentage of products replaced during the warranty period of the cars. In truth, the supplier in analyzing the returns disputes the non-conformity of the pieces received back. The joint analysis between the supplier and the manufacturer therefore does not reveal uniformity of views and the pieces analyzed are not completely documented. For example, the mileage charged, the actual period of operation between installation and disassembly are not well known and there is no information on the operating conditions of the vehicle. Finally with the shock absorbers already disassembled and to avoid further legal disputes with the manufacturer, the supplier ends up accepting the actually compliant parts as well and consequently the reversal from the turnover. Not happy with this situation, the supplier decides to equip himself with a Flying doctor to go around the dealerships that declare cars with dead shock absorbers to check their actual state of health. In the first analysis it is highlighted that the request for replacement is concentrated in the period close to the end of the warranty and it is therefore decided to follow this lead carefully. But with the indication of the Flying doctor it is also highlighted that these replacements focus on a specific number of dealerships / services. Once the field of occurrences to be placed under inspection is narrow, the supplier's Flying doctor obtains from the manufacturer's inspector that those specific dealers/services must wait for the arrival of the Flying doctor before being able to replace the shock absorbers on cars 6 months after the end of the warranty.
All this made possible to show that about 70% of the shock absorbers analyzed were compliant and therefore did not require replacement.
• The second case is borderline paradoxical since the subject involved is a well-known engine supplier belonging to the same industrial group as the manufacturer. The engine supplier is contested by the manufacturer for an increase in cases of oil leaks from the engine sump. The engine supplier, accepting the reports as true, begins an in-depth internal analysis to find out the cause of the oil leaks. He repeatedly checks with the hot test technique, but cannot detect the problem. He checks the matches of crankcases and oil sumps without detecting anomalies on the mating surfaces and on the sealing gaskets. Analyzes the project drawings for a long time and makes further improvements to ensure the tightness of the closure. In short, no matter how much effort is made, the reports of oil leaks from the sump not only continue but actually increase in the number of cases. Up to that point, the engine supplier acts only on the manufacturer's report, considering them true also in consideration that both are part of the same industrial group. Only when the engine supplier decides to use its own Flying Doctor can the complicated situation be resolved. The first thing that the Man in the Van takes in charge is to collect the documentation of the cars involved in the engine sump oil leak and he immediately realizes that there are no cars that arrived in the workshops with that single problem, but they were cars that in most cases arrived in the workshop for the periodic service and that in the acceptance form report the leakage of oil from the engine sump among the reported defects. This seems strange right away since the oil leak from the sump is a clearly visible problem when you move the car from the parking lot. Why does wait for the coupon to report this problem? The Flying doctor therefore decides to focus on those workshops / services that have the highest percentages of car returns with oil sump leaks and asks to be immediately notified in order to be able to map the areas of leakage and the conditions of the sealing surfaces and the gasket. But at this point here is the second anomaly. From the same workshops/services that until then reported dozens of cases every month, no more reports are received of cars returning with the problem of oil leaking from the sump. In more than 3 months there is only one case, but as a single defect and not connected to the maintenance coupon. Basically the defect/service correlation, which until then represented 90% of cases, disappears. At that point the suspicion that the numbers previously declared are not true becomes concrete and we begin to investigate those reports. It then turns out that some owners of the cars involved, at the time of acceptance, had not reported the oil leak from the sump and that it was the receptionist who independently entered the item on the acceptance form. It seems evident that the Man in the Van was faced with false reports of the defect which allowed the workshops to charge about 2 fictitious hours of work to be paid by the manufacturer.
These are obviously two borderline cases that do not compromise the work done by the vast majority of suppliers who, as honest operators with great technical skills, help vehicle owners and manufacturers on a daily basis with their work. At the same time, however, these two cases place the accent on the Flying doctor in the automotive sector who, with great commitment and sacrifice, analyze, moving from one part of the territory to another, even cases of great complexity and provide useful indications for solving them. The Man in the Van are, therefore, a valuable, available and highly qualified resource that every supplier should turn to.